
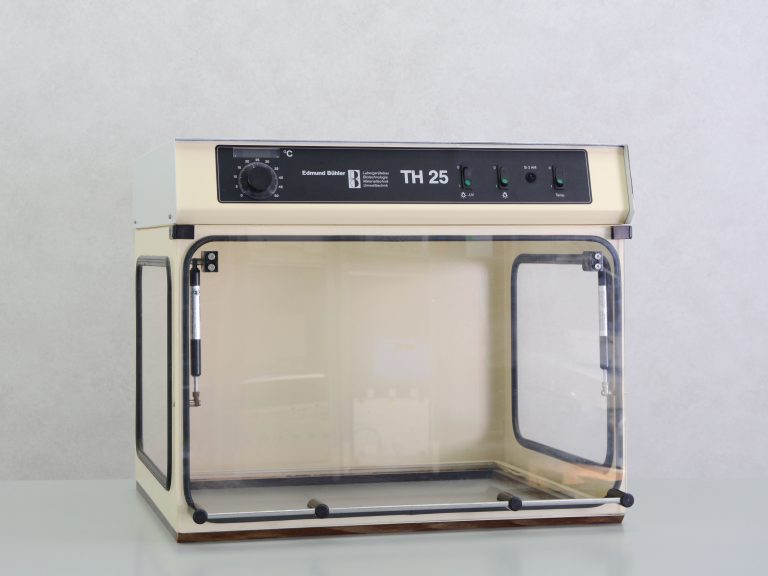
To facilitate fabrication, the functional surface was separately prepared on a large PDMS area, which was subsequently cut and attached to the unibody. The three-channel configuration enables one to measure an unknown sample and the two limits of the calibration range, which in that case was configured to resolve the lower limit of H 2O 2 in urine for whole body oxidative stress monitoring, an indicator associated with the development of numerous serious conditions, such as cancer and heart failure. The ULOC integrates printed connectors ( Figure 2b) that can directly plug into standard silicone tubing (in this case, prepared for 1.5- mm inner diameter tubing), either for continuous flow operation or for pipetting of fixed volumes.

The 3D printed unibody solves several demanding fabrication aspects in a single procedure that takes about 10 min (depending on the printer settings). Figure 2a corresponds to a three-channel design configured for H 2O 2 fluorescence detection on a microscope stage. Figure 2 collects demonstrated examples of such integration possibilities. The process is repeated until completing the printout, which retains in its bottom surface the Teflon texture captured in the last exposure.īesides its simplicity, versatility and economy, the possibility to integrate specialized 3D geometries and to host established LOC configurations are other important aspects of ULOC. ( d) The printout base is raised another 50 μm, and a third layer is exposed. ( c) The printout base is raised 50 μm, and the next layer is exposed, binds to the previous layer and adheres through this to the metal base. Both cured layer surfaces copy the surface textures of the metal and Teflon, respectively. A 50-μm gap between the Teflon surface and the printout base is set, and upon exposure, the far side of the layer sticks to the metal surface of the printout base. ( b) Cross-section of ( a) indicating the first printed layer. Liquid resin in the tank is confined between the printout base and the tank bottom, which is a transparent Teflon film. The illuminating pattern is provided by a digital micro-mirror device (DMD), which defines the x-y resolution of the UV exposure. ( a) 3D scheme of a generic stereo lithography (SL) printer arrangement. In this case, the layer binds to the previous cured layer, and the process is repeated for subsequent stacking planes ( Figure 1d). In the next step, the base is raised by 50 μm, and a new exposure occurs ( Figure 1c). When the resin is exposed (4 to 10 s, depending on the design), it cures through the gap and adheres to the surface of the metal base, capturing its texture in the printout, whereas the side in contact with the Teflon film does not adhere to the surface, but yet captures its surface texture. Initially, the base is positioned at 50 μm from the Teflon surface, leaving a gap entirely filled with liquid resin ( Figure 1b). Figure 1b,c describes the 3D build-up of the printout.
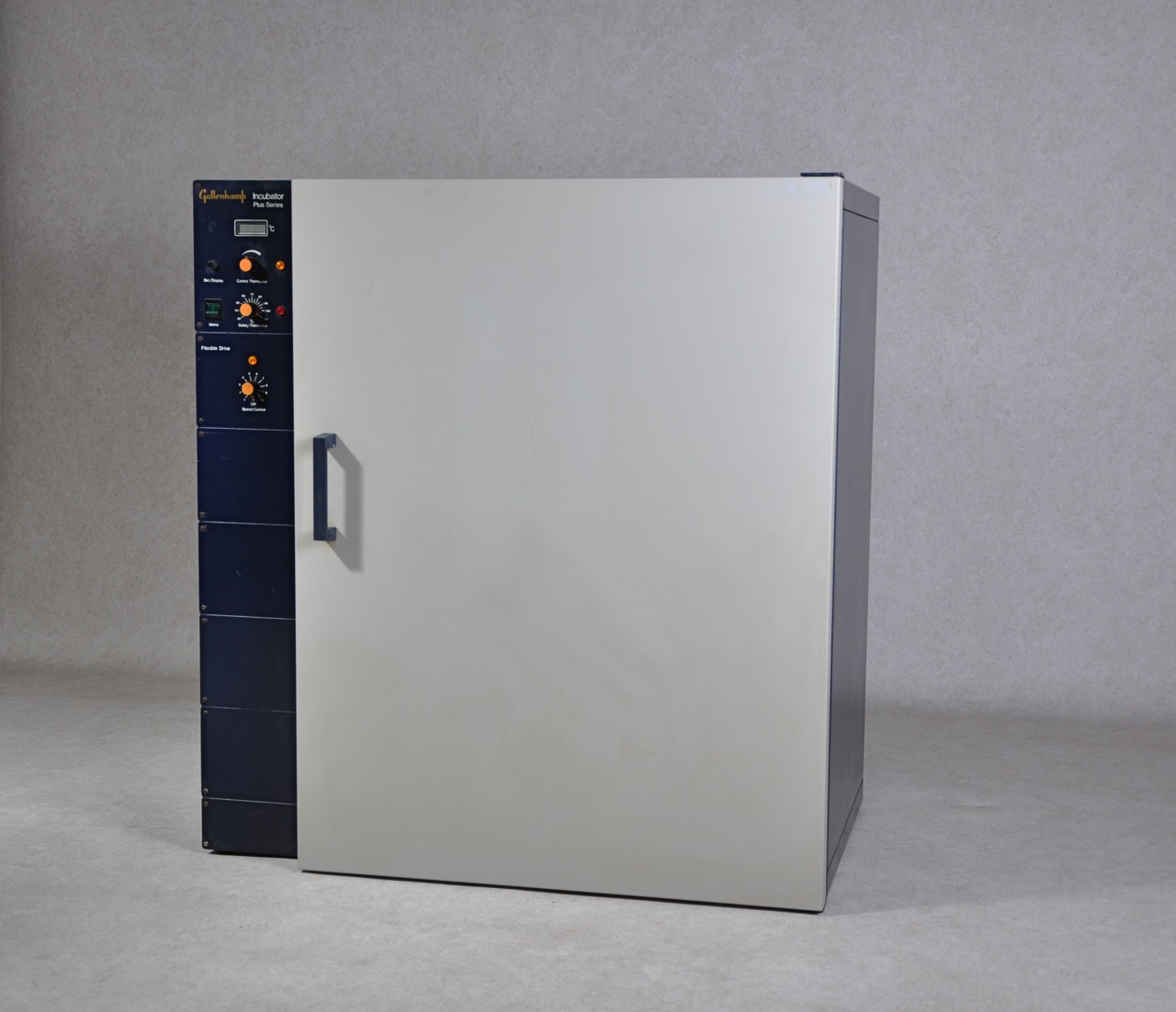
The printout emerges adhered to a metal base that the printer positions in the z-axis at 50-μm resolution. The bottom of this tank is a 127 μm-thick Teflon film (DuPont™ Teflon ® FEP film, Dupont, Wilmington, DE, USA), stretched by contact with a quartz glass (not indicated in the figure). A tank with a transparent bottom holds the printing resin in liquid form. Please click on a product title for detailed information and picture, or browse the Categories page.Figure 1a shows the spatial arrangement of the printer parts. You can scroll down to view the inventory or use Search box to search for keywords. This page represents our entire inventory sorted by manufacturer#8217 s name.
